Slashing embodied carbon in buildings webinar and why Atlassian’s new headquarters could be a game changer
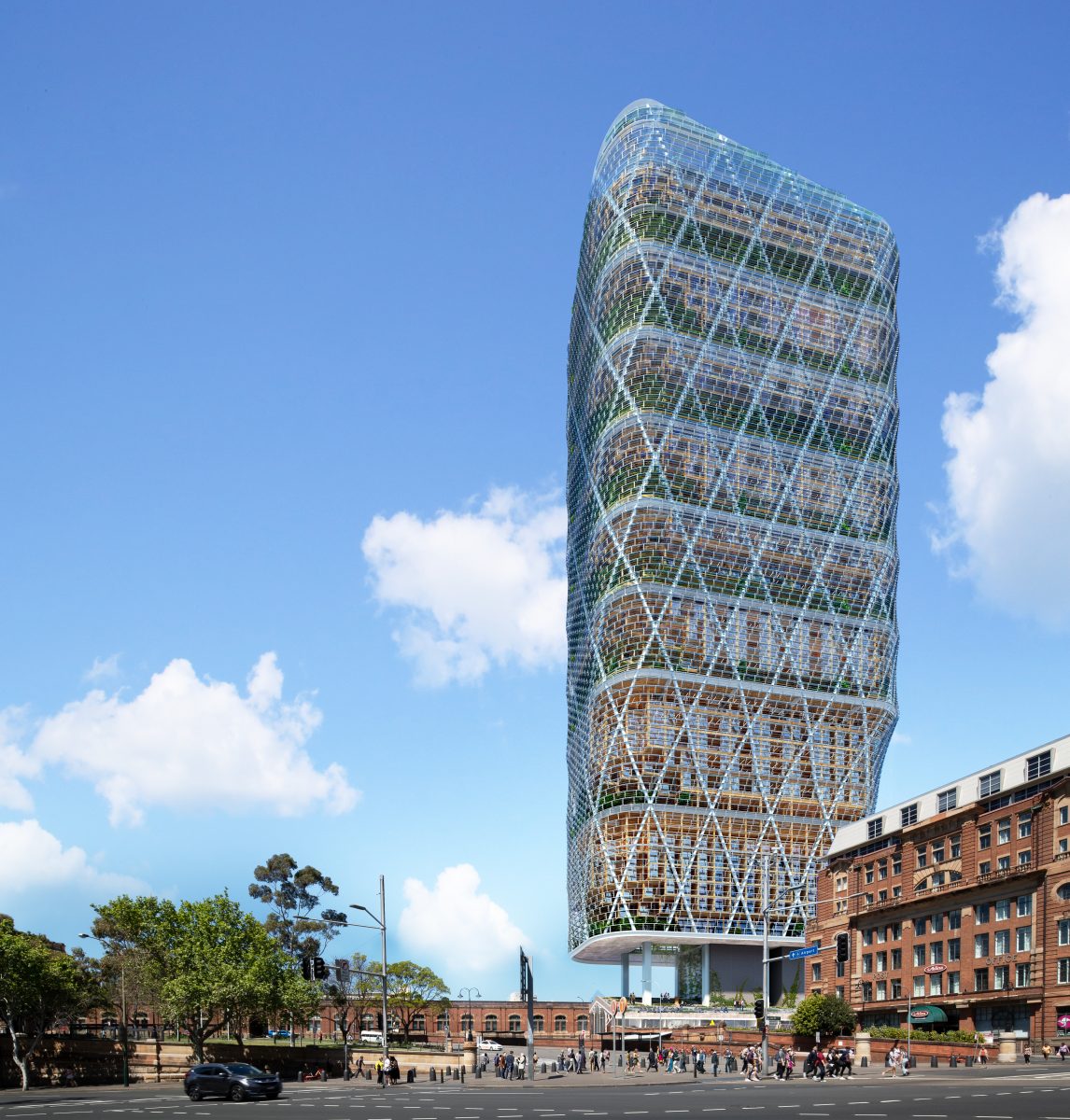
The innovators at the centre of Atlassian’s exciting new Sydney headquarters, including Built, joined the Fifth Estate this week for a webinar discussion on the issue of embodied carbon.
Embodied carbon may be the next, and most difficult, frontier for our industry on the road to reducing building emissions.
A landmark project in that journey is set to be Atlassian’s Sydney headquarters, aiming for 50 per cent the embodied carbon of a conventional building, it will achieve with the help of construction firm, Built, as well as over 40 separate consultants spanning nine time zones and 11 different locations.
Atlassian project director, Bronwyn Zorgdrager said from the start, sustainability was almost as central to the process as budget — with several targets, of which embodied carbon was proving the biggest challenge.
The building’s design is by necessity quite unique, partly due to the heritage listed “parcel shed” that will make up its lobby. Its core is concrete down to the basement which provides stability, surrounded by a steel mega frame and timber exoskeleton and internal office spaces.
“Low embodied carbon specification for both concrete and steel is constantly being monitored as we move through this process and we’re looking to pull out materials where we can and looking at green procurement opportunities,” Ms Zorgdrager said.
“Mass timber is another big one. This building is the tallest tower that’s ever been built in Australia for timber and we’re looking to maximise the use of that, so we’re looking at replacing traditional concrete with timber where we can.”
The contractor controls that supply chain and is best placed to influence a lot of sustainability outcomes
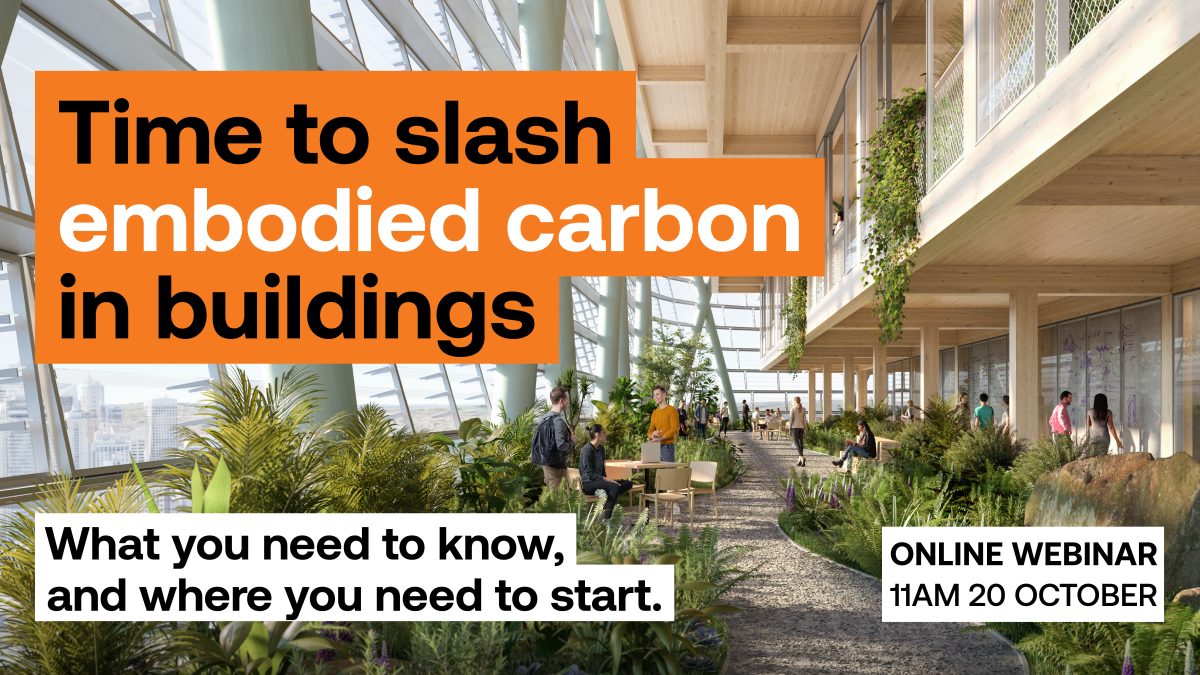
Being at the centre of the materials supply chain, Built chief executive and director, Brett Mason said builders and contractors had an active role to play in building a super sustainable project like Atlassian’s.
“While it’s absolutely imperative that the client sets the sustainability vision for a project at the start, at the end of the day it’s the contractor who controls that supply chain and is best placed to influence a lot of sustainability outcomes,” Mr Mason said.
Within that sits the difficult target of embodied carbon, which makes up around 11 per cent of global carbon emissions — next to the roughly 29 per cent of operational carbon, which is more widely understood and in the process addressed by the industry
“As operational carbon gets driven down to net zero, all of a sudden that 11 per cent is going to be a bigger piece of the pie,” he said.
On the positive side, cost does not have to be prohibitive to reducing embodied carbon. Mason gave the example of Boral’s ENVISIA concrete which he said came with large carbon savings at a low additional cost.
One of the challenges with tackling the relatively uncharted territory of embodied carbon is a lack of data and baselines to work from.
“I think we might be heading towards something like kilograms per square metre of floor area or something like that but ultimately I think we’ll see maybe the Green Building Council or MECLA providing the platform for that knowledge sharing,” he said.
Tasked with tracking and quantifying the embodied carbon savings in Atlassian’s building is head of sustainability and social impact at Built, Joe Karten and LCI consultants principal, Matt Williams.
The Fifth Estate’s mission is to help fast track climate action and sustainability, starting with the built environment.
Please consider supporting us by becoming a paid member and join the biggest, most exciting collaborative network on the planet, all working towards a better future.
Mr Karten said from the start choosing a baseline or reference case if taking a percentage reduction approach was important and echoing what Mr Mason said, make the party with the greatest ability to manage the materials supply chain accountable for measuring and reporting savings.
“We think it’s really important to use best practice methodologies to measure those savings. You really do need to be able to compare apples to apples with other buildings. We use industry tools like eTool but we also rely heavily on environmental product declarations (EPD),” Mr Karten said.
Mr Williams agreed it was increasingly vital for companies to include EPDs with their products to give those further down the supply chain a clearer idea of how to achieve embodied carbon savings.
“Keep pumping out those EPDs because they are the lifeblood of this, they are the nutritional information box on the side of your cereals so without that we can’t really make informed decisions,” he said.
Williams also specified that what he was primarily concerned dealing with was upfront embodied carbon as opposed to what was occuring down the track.
“There’s a lot of debate around biogenic carbon and the idea that the end of life for material use is super critical, and of course that’s true, but that can sometimes be used as a lever against making some things that just make sense.”
We heard plenty more from these speakers as well as New Zealand Green Building Council chief executive Andrew Eagles who spoke about new carbon standards that will be embedded in the country’s building code coming soon. The NZGBC will shortly consult on the measurement of embodied carbon, thresholds for different building types and how to incentivise lower embodied carbon buildings, he said. From Turlough Guerin from the NSW government we heard about exciting programs he’s working on in partnership with industry around low embodied carbon materials.
This article was first published by The Fifth Estate and has been published with their permission.